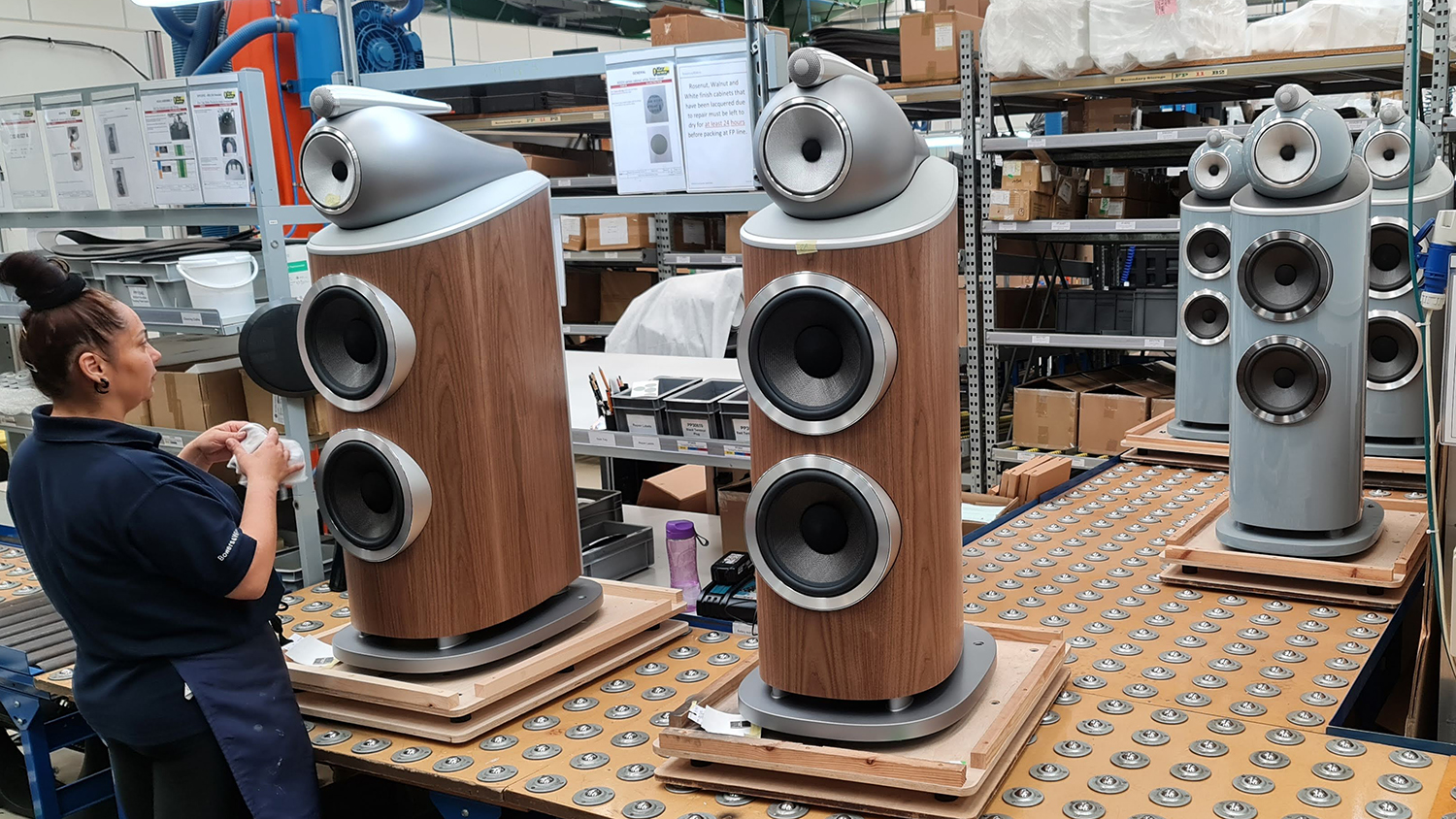
Bowers & Wilkins is a speaker company like no other. Not only does the brand have a global reputation that's arguably unrivalled, it also makes speakers in its native UK on a scale that nobody else can match.
While many of B&W's speakers are now manufactured elsewhere, the flagship 800 Series are manufactured – give or take a few smaller pieces – and assembled at the company's Worthing factory on the south coast of England.
And for 2021, we have a whole new range: the 800 D4 Diamond Series. The new 800 Series is still seven strong, with the two-way 805 D4 standmounter joined by the 804 D4, 803 D4 and 802 D4 three-way floorstanders, HTM81 D4 and HTM82 D4 centre channels (for home cinema use) and the brand-new flagship 801 D4 floorstander (which replaces the existing 800 D3).
Alongside the Continuum cone and Diamond tweeter, there's enhanced Matrix bracing, a Reverse Wrap cabinet design, updated Solid Body Tweeter-on-Top housing and a completely upgraded motor system. You can read about all the 800 D4 upgrades in our news story.
But for now, let us take you behind the scenes and show you exactly how these speakers are made, straight from the factory floor in Worthing.
B&W 800 cabinets
The basic raw material for the B&W 800 cabinets are sheets of beech wood. Multiple layers arranged in an alternating grain structure are used to add extra stiffness to the panel.
Dried glue holds the layers together and this is then heated and the panel bent into shape on a forming press. And the cabinet shape begins to appear.
The latest hi-fi, home cinema and tech news, reviews, buying advice and deals, direct to your inbox.
A cutting machine then precisely cuts the wood into the right shape to begin to form the cabinet. The precision of the machined cuts is crucial. Every element must exactly meet the next, whether that be another wood part or metal. If at any point you get variables – any less than perfect contact – it's a weakness. That's why a robot gets the job. However, everything is still checked and measured by hand at this point, so any issues can be corrected before the fledgling speaker gets any further along in the process. The tolerance? 0.2 millimetres.
Upgrades to the factory means that there are now five presses, ensuring the factory can make all five B&W 800 Series speakers at the same time, with no need to batch build as they used to have to do.
You'll notice all the new 800 Diamond models now have the Reverse Wrap design, meaning the joints in the cabinet are now at the back, at the furthest point away from the mechanical energy generated by the drivers.
Next it's time for... "the spreader". This allows the cabinet to be prized apart and the necessary internal components to be installed inside.
The main element to be added is a wooden lattice arrangement, which reinforces the cabinet in all directions. In this new generation of 800s there are now metal elements included in this matrix to further add to the overall rigidity. Why not make it out of just metal? First, this would create a more resonant structure. Secondly, metal with the wood outer skin just doesn't work so well.
The fledgling cabinet then moves to a setting chamber where it will remain for two hours. It's then removed from the supporting jig and allowed to settle for a further two hours. At that point the cabinet can move to the next stage of production.
In the previous generation D3 800 Series the crossover used to live in a box at the bottom of the cabinet. This vibrated. So B&W has moved to a solid metal plinth, which is mechanically much quieter. As a result, the crossover had to be moved. Now it's in a space in the back of the speaker on all the new 800 D4 Series speakers.
Sanding and painting
Next it's time for the cabinet to move to the sanding area. The robot does the heavy lifting, doing 90% of the sanding, with the rest done by hand. The robot follows a programme specific to each speaker, ensuring not just that the correct areas are covered but that the level of pressure is correct. Skilled workers check and finish the sanding process by hand.
Now the cabinets are ready to be in turn painted and baked. The paint robot will apply four coats of paint from the robot paint sprayer, the speakers are then buffed by hand, before going back through the robot to get more paint.
Should any issue be spotted during this whole process, the cabinet is rejected. If aesthetic issues can be picked up early, the cabinets can be sanded back again and re-enter the production line.
Wooden cabinets move around the factory as a pair, complete with a birth certificate, so if any cabinet is rejected it means both cabinets being taken off the production line. B&W says issues are spotted on around five to ten speakers per week.
This birth certificate is matched to a serial number on every finished speaker, ensuring every pair of speakers can be tracked back to a specific day of production; handy if any post-sale issues arise.
B&W 800 D4 drivers
The 800 D4 speakers use the same drive unit materials but a completely new motor system.
We check out B&W's famous Continuum cone being manufactured, too, though pictures aren't allowed here and the exact substance and processes involved remain tightly under wraps. "So you're not just using PVA glue from B&Q?" we ask as we watch the manufacturing process. It seems not...
Rigid but flexible is the name of the game, with B&W making the move from Kevlar once it was happy Continuum could do an overall better job.
A thin membrane of smooth diamond makes the tweeter. Yes, real diamond. It's artificially-grown by the famous De Beers diamond company not far away in Berkshire.
Back in Worthing, B&W assembles the dome with its own coils, then the surround, diaphragm mounting plate and the magnet. This then joins the milled aluminium tweeter assembly.
Once fully assembled it's of course checked and tested before being installed in the cabinet.
Crossover boards are all built to spec by hand on site, tested and then signed-off, before heading down to the assembly line.
The 803 D4 features Mundorf MCap and EVO capacitors, the 802 D4 doubles up on the MCap alongside an Evo, while the 801 D4 has the MCap Supreme Silver/Gold/Oil. The crossover boards then head downstairs to be put inside the speaker.
Tucked slightly away from the main action we find an area dedicated to work being done by hand. There's more painting and sanding, dedicated to ensuring the level of quality required, especially with some more awkward components, such as the metal turbine head used to house the midrange of the larger floorstanders. Also: this is a very awkward shape for a robot.
Final assembly line
You'll notice the rogue battleship grey speakers in the background on the final production line. These are the line references. These are finished prototypes brought back from the sound labs, painted a different colour so they don't get lost, and used to recalibrate the test chamber (pictured, below) every month to make sure the assembly line is making the right product.
Interestingly, none of the workers use gloves, the company having realised the human touch is the best way to do the final fit without any drops or breakages. A final clean is of course required to remove any fingerprints before they're packaged up and ready for a lucky punter.
The business of making speakers isn't just about turning out great speakers, you need to be able to deliver the speakers, in quantity, to dealers and customers. That's why this B&W factory has space for more than 5000 pallets.
Elsewhere, we see testing rooms for items such as screws, which Bowers doesn't deem it necessary to make, so the parts are batch tested at a rate of 1 in 10 items. If there are any issues, this jumps to every item. Any further issues and it's probably time for a new supplier.
Most of the parts that are delivered by outside suppliers come from as close to the factory as possible, though there are still some specialist items that are made in China to a quality level that B&W can't find in the UK.
B&W Nautilus
We turn another corner and find a couple of guys working alone in what feels like a secret corner of the factory. Here, it's all about the famous B&W Nautilus – no doubt many people's choice as the ultimate speaker of all time.
Nowadays the famous cabinets take the form of three sections, a front, plus left and right sections. These have to be joined together and painstakingly sanded to manage away any visible edges. Paint is sprayed by hand – typically, with 12 coats of paint and lacquer.
The Nautilus cabinet moulding is made here (it used to be manufactured off-site but is now in-house). One Nautilus shell takes a whole week to make, with three days of final polishing to get to the required finish quality.
We're told there's an almost constant backlog of orders for the B&W Nautilus, despite the price tag that's just shy of £60,000, so if you're thinking of placing an order then it's a case of the sooner the better!
Are these speakers, first unveiled in 1993, in line for an update? Certainly while B&W say they remain excellent acoustically, there's no denying speaker engineering has moved on significantly. How about a 30th anniversary special? We'd certainly love to see what the B&W engineers might come up with now to reimagine arguably B&W's most famous speaker.
On a related note, we're told the research team is always working on refinements and upgrades for the 800 Series, it's simply a matter of timing as to when certain updates make it into the final speakers.
And things move fast. Back in 2008/09, only the drivers on the speakers were FEA (finite element analysis) optimised. Now, every element of the speaker is, with greater accuracy and at faster speed.
B&W listening rooms
A few minutes down the road, the original B&W factory is now transformed to a versatile office space, complete with multiple listening rooms – and we get a chance to, briefly, hear two of the new models.
And it's the two speakers that, if previous generations are anything to go by, will likely prove to be the best-sellers: the 805 D4 bookshelf speakers, the smallest in the range, and the 804 D4, the entry-level floorstanding speaker. Perhaps no surprise, considering they're the most affordable and easiest to accommodate.
Listening to B&W's systems, it's hard not to enjoy ourselves. But when it comes to making a considered final judgement, we'll wait until we can listen for an extended period in our listening rooms and publish a full review.
The full B&W 800 Diamond D4 range is on sale now, having been in stores from 1st September. The flagship 801 D4 heads the line-up and costs £30,000 ($35,000, AU$52,900), with the 802 D4, 803 D4 and 804 D4 floorstanders following at £22,500 ($26,000, AU$38,900), £16,000 ($20,000, AU$29,900) and £9500 ($12,500, AU$18,900) respectively. The 805 D4 standmounters are priced at £6250 ($8000, AU$11,900), with the dedicated FS-805 D4 stand costing an extra £1100 ($1200, AU$1799).
Finally, the HTM81 D4 and smaller HTM82 D4 centre channels are priced £6500 ($7500, AU$11,500) and £4750 ($5500, AU$8500) respectively, with the matching FS-HTM D4 stand costing £700 ($800, AU$1199). Prices are up around 10% on the previous generation with B&W, naturally, happy that the increases are fully justified by the improvements in build and performance.
We hope to find out for ourselves sooner rather than later...
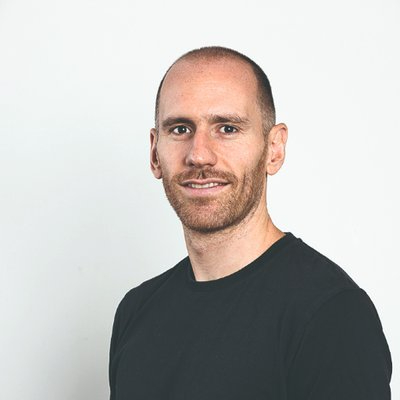
Joe is the Content Director for What Hi-Fi? and Future’s Product Testing, having previously been the Global Editor-in-Chief of What Hi-Fi?. He has worked on What Hi-Fi? across the print magazine and website for almost 20 years, writing news, reviews and features on everything from turntables to TVs, headphones to hi-fi separates. He has covered product launch events across the world, from Apple to Technics, Sony and Samsung; reported from CES, the Bristol Show, and Munich High End for many years; and written for sites such as the BBC, Stuff and The Guardian. In his spare time, he enjoys expanding his vinyl collection and cycling (not at the same time).